As the understanding of process safety has increased over the last few decades, countries' health and safety legislation has also been updated. There is a general trend to changes in the wording of legislation from talking about identifying and understanding hazards to eliminating or minimising risks. The question is what does that look like in practical terms and how far should it be taken?
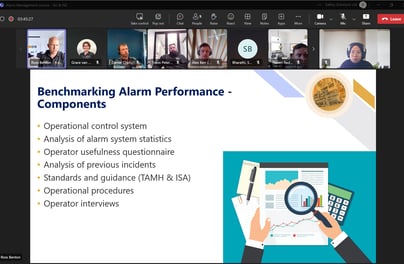
Understanding the risks of the plant still starts with some kind of Hazard Identification process. This will be in the form of a Hazard and Operability Study, a Process Hazard Review or similar. The type of review will depend on the complexity of the process.
The risk assessment process then has two inputs, likelihood identified events and the severity of the consequence.
Assessment of Consequence – The assessment of the consequence should consider the level of impact on people and the scale of that impact i.e. how many people will be affected and how badly. Consequence assessment will be a topic of future blogs.
Assessment of Likelihood – For the assessment of likelihood several techniques should be considered depending on the complexity of the plant equipment and the severity of the consequence, as per the table below.
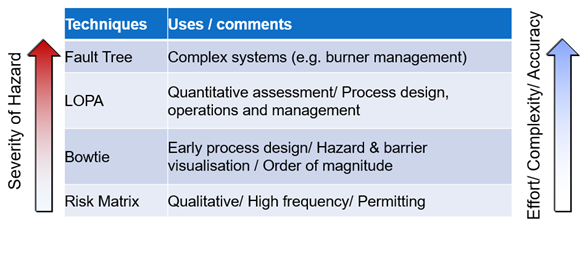
Risk Matrix and Bowtie are both considered qualitative assessment methods. These are used when controls are mainly administrative (Operating procedure, Permit to Work etc.). Due to the nature of administrative controls, risk reduction is very subjective and strong rules should be in place to estimate where the mitigated risk falls on the risk matrix. These methods are also reliant on a Risk Matrix that has been appropriately calibrated for Process Safety (See the link below to download our paper on how to calibrate a risk matrix).
LOPA is considered to be semi-quantitative. It uses a simplified cause-to-consequence threat line and real-world frequency data to give a calculated likelihood of the risk after considering the controls in place. Causes can be either human error or equipment failure both of which can use industry data to establish initial likelihoods. Controls are usually engineered automatic responses that have an established probability to fail when they are required to act.
Fault Tree is a quantitative method that considers all the failure paths of a complex process and how they interact with each other to arrive at a final consequence. As with LOPA, Fault Tree uses real-world data to calculate the risk.
Therefore, the answer to the question depends on the degree of harm the Hazard can cause and the type of available controls to reduce the risk.
If you are interested in our risk matrix design/ troubleshooting paper, click the following link: Download Risk Matrix Design Paper
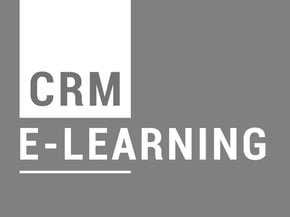
|
|
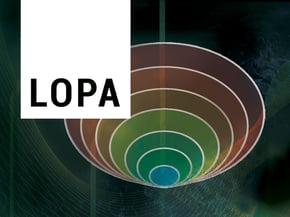
|
THIS E-Learning CRITICAL RISK MANAGEMENT is for Directors and Executives. |
Find out about our upcoming in-person BOWTIE Training Course HERE! |
Our 2-day LOPA Training Course is IChemE approved, find out more HERE! |